Hardness Testing: Ensuring Material Strength and Durability
At SIMIC Manufacturing, we understand the critical role of hardness in determining the reliability and longevity of mechanical components. Hardness testing is essential for evaluating a material’s resistance to surface deformation and its ability to withstand wear, abrasion, and pressure. By carefully controlling and measuring hardness, we ensure that all our products meet the high-performance standards required by our customers.
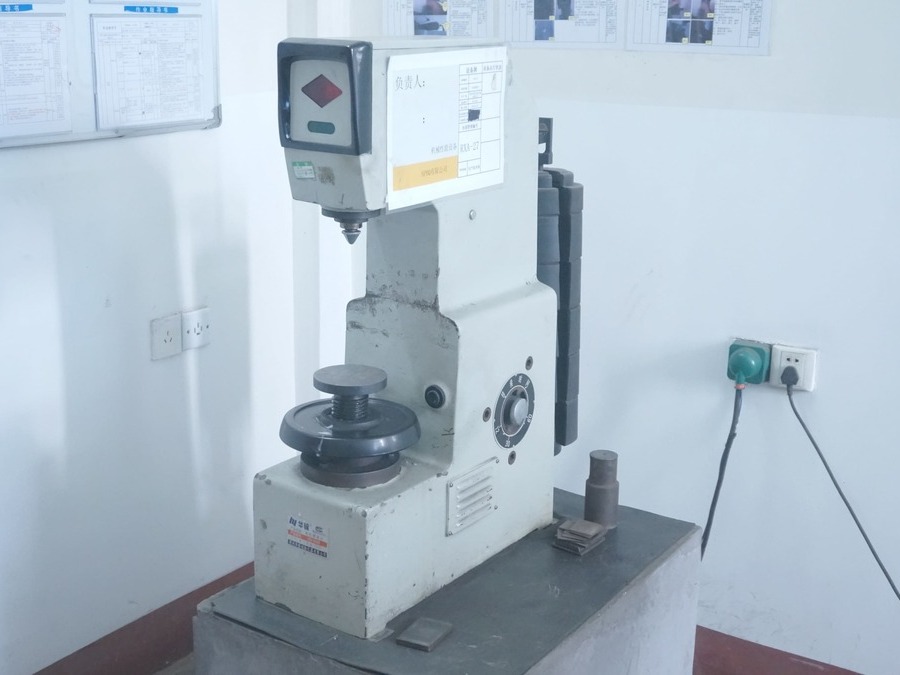
Why is Hardness Testing Important?
Hardness testing provides invaluable insights into a material’s overall strength, durability, and wear resistance. The hardness of a material is often correlated with its mechanical strength—higher hardness typically indicates stronger materials that can better withstand mechanical stress. Understanding hardness is especially crucial in the manufacturing of components for automotive, aerospace, construction, and heavy machinery industries, where material failure can result in costly downtime or safety risks.
Key reasons why hardness testing is integral to our quality assurance process:
- Performance Assurance: Materials with the right hardness values are more likely to perform well under operational stress, ensuring that products function as expected over their service life.
- Improved Machinability: The hardness of a material affects its machinability. Soft materials are easier to machine, while harder materials can be more challenging but may offer superior performance.
- Cost Efficiency: By controlling the hardness of our products, we optimize manufacturing processes, reduce scrap rates, and improve the overall cost-effectiveness of production.
Our Rigorous Approach to Hardness Testing
To meet the strictest quality standards, we employ a comprehensive approach to hardness testing, ensuring that every product we produce complies with both ISO 9001 and IATF 16949 quality system requirements.
- Strict Material Inspection: Before testing hardness, we ensure that the incoming raw materials meet our rigorous specifications. This involves detailed inspection of chemical composition, mechanical properties, and surface conditions.
- Advanced Testing Equipment: Our hardness testing is performed using state-of-the-art testing instruments to ensure precision and reliability. We utilize a variety of methods including Brinell, Rockwell, Vickers, and Leeb testers, depending on the material type and application.
- Systematic Testing and Recording: We adhere to standardized testing frequencies and procedures, with all results being meticulously recorded and archived in compliance with our quality system. This ensures traceability and allows us to maintain a consistent record of the materials’ properties throughout the production lifecycle.
- Continuous Monitoring and Control: Hardness testing is conducted at multiple stages throughout production, ensuring that every batch meets the required hardness specifications before it leaves our facility.
Types of Hardness Testers We Use
We employ several types of hardness testers, each suited for specific materials and applications:
- Brinell Hardness Test: Ideal for materials like cast iron and alloys with a rough surface, the Brinell test uses a hardened steel or carbide ball to measure the indentation made by applying a specific load. The diameter of the indentation determines the hardness. It’s particularly useful for large, coarse-grained materials.
- Rockwell Hardness Test: The Rockwell test is quick and provides reliable results. It is widely used for metals such as steel, aluminum, and brass. Depending on the material and load, different scales (e.g., HRB, HRC) are used to measure hardness. Rockwell is perfect for in-line testing and mass production.
- Vickers Hardness Test: For precision testing of thin materials and coatings, the Vickers test uses a diamond pyramid indenter. The hardness is determined by measuring the diagonal of the indentation. It is highly accurate and can be used on a variety of materials.
- Leeb Rebound Hardness Test: This portable tester is ideal for on-site testing of large, heavy components, such as those in automotive and construction machinery. The tester measures the rebound velocity of a special impact device, providing quick hardness readings without requiring sample preparation.
Each tester offers unique advantages depending on the material and specific testing needs, ensuring that SIMIC Manufacturing can provide precise and reliable results for every product.
Hardness and Strength: A Correlation with Quality
While hardness and strength are related, they are not synonymous. Hardness is a measure of how resistant a material is to deformation, while strength refers to its ability to withstand applied force without breaking. However, there is a strong correlation between the two: materials with higher hardness typically exhibit greater strength, making them more durable and less prone to wear.
For example:
- Ductile Cast Iron and Gray Cast Iron typically show a relationship between hardness and tensile strength, where a higher hardness correlates with higher strength and better resistance to wear.
- Steel Alloys used in automotive and industrial applications are carefully adjusted to achieve an optimal balance between hardness and strength to ensure reliability under high stress and load conditions.
Hardness Testing Standards and Compliance
At SIMIC Manufacturing, we adhere to the highest industry standards in hardness testing, including ISO 9001 and IATF 16949, to ensure that every product we deliver meets the required quality specifications.
- Frequency of Testing: Hardness testing is conducted at various stages throughout the production process to ensure consistency and reliability. We follow rigorous testing schedules and document all results as per quality system requirements.
- Documentation and Archiving: All hardness test results are carefully recorded and stored for traceability, allowing us to track each product’s performance characteristics. This documentation supports ongoing quality control and continuous improvement efforts.
- Calibration and Traceability: To maintain accuracy, all hardness testing equipment is regularly calibrated against certified standards, ensuring that our measurements are always precise and consistent.
Hardness and Machinability: Impact on Production
Hardness plays a critical role in determining the machinability of a material. Softer materials tend to be easier to machine, but may not offer the same durability as harder materials. Harder materials, on the other hand, offer superior wear resistance but can be more difficult and costly to machine.
By carefully controlling the hardness of our products, we optimize both machinability and durability, ensuring that our components are easy to process while also capable of performing under demanding conditions.
Contact SIMIC Manufacturing
Hardness testing is an essential part of the manufacturing process at SIMIC Manufacturing. We use a variety of advanced hardness testing methods to ensure the performance, durability, and machinability of every product. With a focus on precision, reliability, and adherence to industry standards like ISO 9001 and IATF 16949, we are committed to delivering products of the highest quality. Whether it’s a large casting, a thin-walled component, or a critical part for the automotive industry, our rigorous hardness testing procedures help ensure that each product is up to the task.