Green Sand Casting Process
Green sand casting is one of the most widely used casting methods, offering versatility and cost-efficiency for producing a wide range of metal parts. It uses a mixture of sand, clay, water, and other additives to form molds into which molten metal is poured to create parts. This process is ideal for producing both simple and complex parts in medium to large volumes. SIMIC Manufacturing employs two main approaches in green sand casting: Hand Molding and Auto-Molding. Both have their unique benefits and limitations, which we detail below.
The Green Sand Casting Process Flow
- Pattern Creation: A pattern of the part to be cast is made from metal, resin, or other materials.
- Mold Formation:
- Hand Molding: The mold is created manually by packing the sand mixture around the pattern.
- Auto-Molding: The automated machine compacts the sand around the pattern to form the mold.
- Core Creation (if required): For parts with hollow sections, cores are created using sand and placed inside the mold.
- Mold Assembly: The two halves of the mold are assembled, with or without cores, depending on the part’s requirements.
- Pouring: Molten metal is poured into the mold cavity and allowed to cool.
- Cooling & Shakeout: The mold is allowed to cool, after which the sand is shaken out to remove the casting.
- Finishing: The casting undergoes any necessary finishing processes, such as trimming, cleaning, and machining.
Hand Molding
Hand molding involves the creation of molds manually by skilled foundry workers. This process is more labor-intensive but offers flexibility in small to medium production runs and complex parts that may require intricate core placements or special shaping.
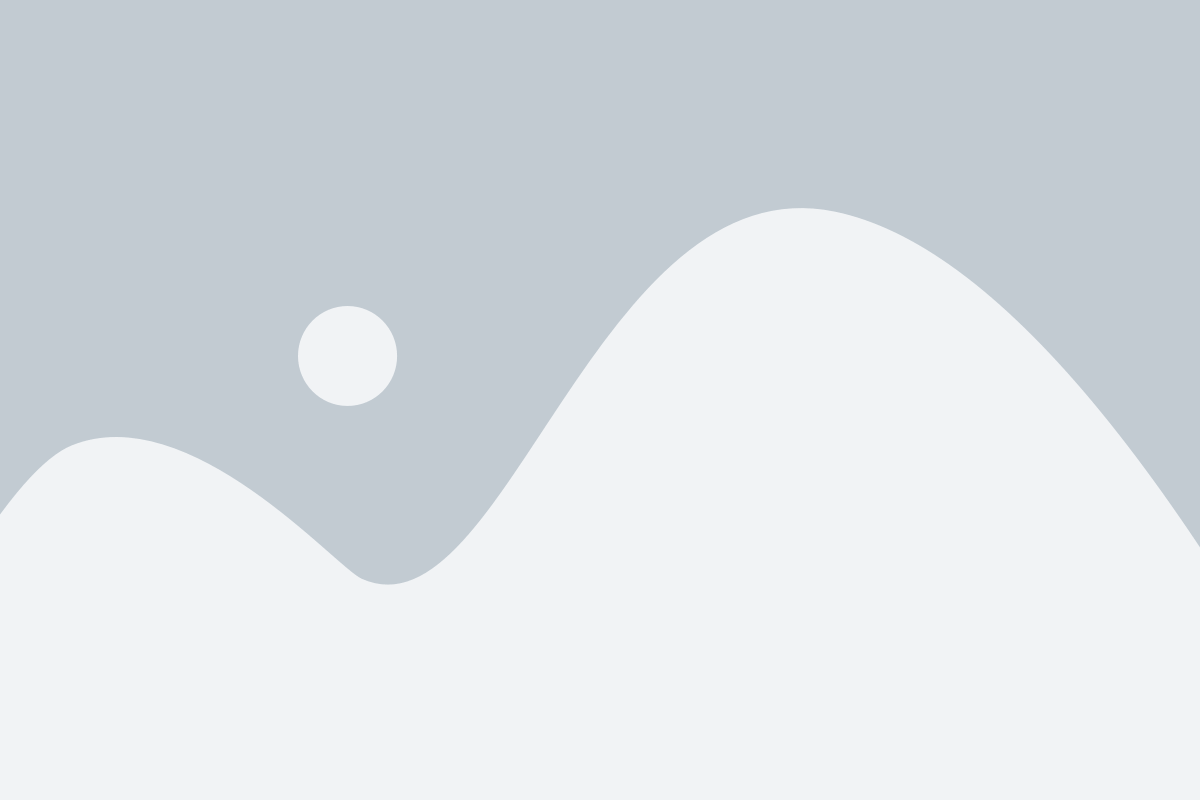
Advantages of Hand Molding
- Flexibility: Ideal for low-volume production and complex, custom parts with unique designs.
- Lower Initial Setup Costs: Does not require expensive machinery or tooling, making it cost-effective for smaller quantities.
- Customization: Allows for more direct adjustments to molds, which can be beneficial for specialized or one-off parts.
- Ideal for Complex Geometries: Skilled workers can address complex designs and difficult-to-machine shapes.
Disadvantages of Hand Molding
- Labor Intensive: Requires skilled workers, increasing the need for more labor.
- Slower Production Rate: Generally slower than automated methods, which limits production speed.
- Limited Consistency: While skilled, manual molding can result in slight variations between parts, impacting uniformity.
- Increased Risk of Human Error: More chances for defects due to the hands-on nature of the process.
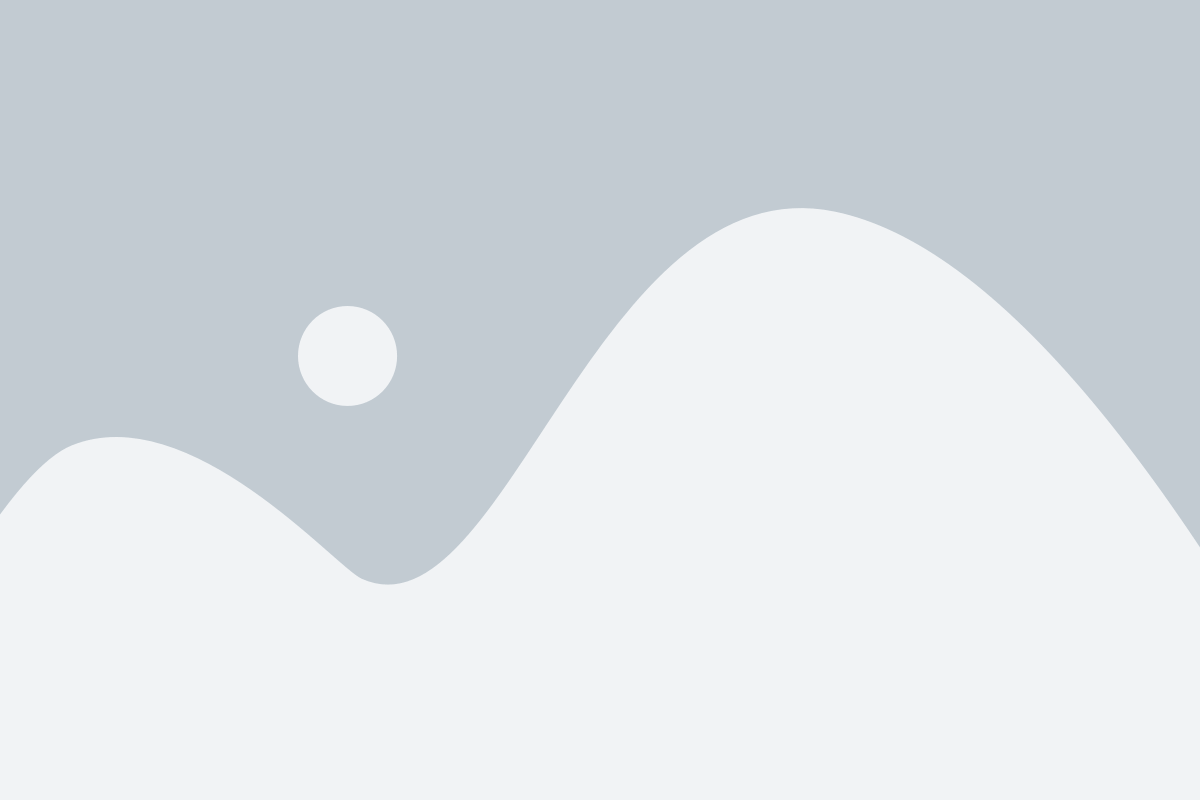
Auto-Molding
Auto-molding is ideal for large-volume production runs, as it offers higher automation and faster cycle times compared to manual molding. This method uses automated equipment to create high-precision molds, making it suitable for medium to large castings, particularly those that require multiple internal cores or complex geometries.
Advantages of Auto-Molding
- High Production Speed: Automated machines significantly increase the speed of mold formation, making it ideal for medium to large volume production runs.
- Consistency & Precision: Machine-based molding ensures uniformity across all parts, producing consistent molds with minimal human variation. This is crucial for parts that need to meet tight tolerances.
- Reduced Labor Costs: Automation reduces the need for manual labor, which lowers overall labor costs and increases operational efficiency.
- Better for Larger Quantities: Auto-molding is more cost-effective and efficient for larger production runs due to the high speed and consistency of machine operation.
- Improved Mold Quality: Automated molding provides a more uniform compaction of the sand mixture, resulting in fewer defects, better surface finishes, and less scrap.
- Less Human Error: The reliance on machines means fewer mistakes compared to hand molding, resulting in higher-quality outputs.
Disadvantages of Auto-Molding
- High Initial Investment: Setting up an auto-molding system requires significant upfront investment in machinery, tooling, and setup costs, which can be prohibitive for low-volume or one-off productions.
- Less Flexibility for Customization: Auto-molding systems are optimized for high-volume production and standard parts, making them less adaptable for highly complex or customized parts that may require manual adjustments or intricate details.
- Maintenance Requirements: Machines require regular maintenance and occasional repairs, which can lead to downtime and additional operational costs.
- Longer Setup Time for New Parts: For new or complex designs, auto-molding machines may require additional setup time to create custom molds, which may reduce the overall speed benefits.
- Limited to Standardized Molds: Auto-molding is not as flexible as hand molding when it comes to producing highly customized or intricate geometries, as it relies on preset configurations and tooling.
Why Choose SIMIC Manufacturing for Sand Casting?
- Versatile Applications: Suitable for a wide range of ferrous and non-ferrous materials.
- Customizable Solutions: Both hand molding and auto-molding methods available for tailored solutions.
- Efficient Production: High-quality, precise, and consistent parts produced at competitive lead times.
- Environmental Responsibility: Up to 70% of the sand used in the process is reclaimed and recycled.